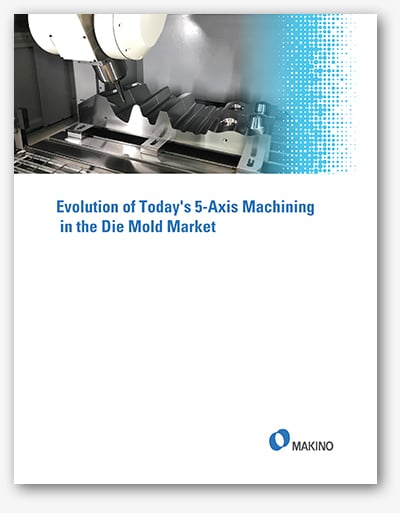
Today’s die mold machining technology has drastically evolved over the last eighty years.
In order to fully appreciate the technological advancements available today, you must first understand how CNC and die mold manufacturing came about, how the technology evolved and why.
In this informative whitepaper, you’ll gain an appreciation for the machines and see the advancements in technology that have improved large die and mold part manufacturing, making 5-Axis what it is today.
Additionally, you’ll discover the tooling and 5-axis software developments that can deliver even greater gains in productivity.
These newfound technologies can reduce the preparation phase by providing a decrease in the time it takes for programming. It can also lessen the number of steps and programs and create a reduction in toolpaths.
In addition to this time-reduction benefit, 5-Axis machining can also minimize the need for blending, matching, and stitching surfaces. Die mold companies that utilize 5-Axis are also able to employ barrel-shaped tools which can minimize the overall number of tools being used and the set-up/handlings involved.
One of the major benefits of 5-Axis technology with die mold manufacturing is the improved access to part geometry with die mold components. This can result in a more uniform and higher quality surface finish which can provide:
- Lower tool costs
- Longer die mold tool life
- Fewer tools required for the project
All of this can lead to significantly reduced cycle times as well as shortened-lead times and more throughput.
Discover the history of 5-axis machining and learn the proprietary developments and enhancements that can create opportunities to better utilize die mold cutting tools and 5-Axis mills and improve your profitability.
>>Download the White Paper>>