The role of the toolholder in high-speed milling is really no different than its role when applied conventionally. The role of the toolholder is always to provide an interchangeable interface between a machine spindle and a cutting tool, such that the effectiveness of either component is not diminished.
In other words, the best possible toolholder cannot make a bad tool cut well or make a worn out spindle run like new. But a bad toolholder can do no harm to a good spindle and will adversely affect cutting parameters, ultimately resulting in premature tool failure.
What makes a good toolholder? At any cutting speed, a good toolholder must:
- Fit the spindle accurately, such that the central axes of the toolholder and the spindle coincide exactly.
- Extend the coincidence of the central axes to include the toolholding feature.
- Provide the maximum rigidity possible consistent with size and other design constraints.
The evolution of high-speed milling technology makes the importance of the fit between the spindle and the toolholder difficult to overstate. This connection between spindle and toolholder is the source of accuracy, repeatability, balance and rigidity in the cutting system. There is no compromise possible in the quality of this connection. The recent update to “V2 Flange Tool Shanks for Machining Centers With Automatic Tool Changers, ASME B5.50-1994, now calls for spindle fit tolerance of AT4 per ISO-1047. The meaning of this coded message is simply that the cone angle tolerance for toolholders manufactured in the United States has been tightened. But is it enough? In the opinion of many, the tolerance should be set to the AT3 cone quality specification defined in ISO-1947 to obtain the improved contact and resulting axial coincidence required. Several manufacturers have thus adopted the tighter AT3 standard for at least some if not all of their toolholder products.
The second point refers to the relative concentricity between the tapered shank and the actual tool holding surface. The goal is obviously to have the tool axis rotating on the exact same axis as the spindle. Displacement of the centerline of the holding feature relative to the centerline of the tapered shank must be held within a maximum .0001" to .0002" to assure optimum cutting. Also, displacement of the cutting tool relative to the spindle axis results in an out-of-balance situation that can affect operation at high speed. Finally, rigidity throughout the entire system is essential. Toolholders are built to rotate a tool on center. Therefore it becomes obvious that machining stresses require a toolholder to not flex or disturb that centrality. Toolholder design should be as robust as clearances allow and as short as possible - especially at high speed.
So far, the desirable features mentioned, namely spindle fit, concentricity and rigidity, apply to any toolholder in any milling operation. However at higher rates of revolution encountered with many high-speed machining applications, a fourth component of toolholder design becomes increasingly importantbalance.
The Balancing Act
At one time or another, most of us have driven a car that had an out-of-balance wheel. Around town, we don’t even notice the problem, but when we hit the freeway, a vibration becomes apparent. If the speed is high enough and the out-of-balance condition bad enough, we will find that our maximum speed will be defined not by the power or aerodynamics of our vehicle, but by the severity of the vibration caused by the out-of-balance wheel.
This analogy extends itself to high-speed milling. The faster the spindle rotates, the more critical the unbalance of the spindle becomes; at today’s racetrack speeds, it’s extremely important that the spindle and the toolholder assembly be balanced to a fine tolerance. Consider a typical out-of-balance toolholder, of which a V-Flange end mill holder, made to print, is an ideal example (see Figure 1).
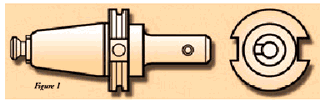
The inherent unbalance will not cause any problem at speeds identified with conventional milling speeds of approximately 4,000 rpm. The same holder at 12,000 rpm, however, may cause the tool to generate a poor surface finish and contribute to premature tool failure and/or a spindle failure. The same holder will probably not allow cutting at 20,000 rpm due to heavy vibration. Because unbalance forces increase as the square of rotational speed, the effect of unbalance at 20,000 rpm is 25 times as great as it is at 4,000 rpm.
Tolerable Unbalance
Having established the need for balanced tools, a consideration of balance quality is in order. Some amount of unbalance is always tolerable. We can qualify and understand this tolerance based on three factors:
- How fast will the tool be rotated?
- To what tolerance is the machine spindle balanced?
- How much does the tool/toolholder assembly weigh?
Because there are a wide variety of high-speed spindles in use, the balance quality of a specific spindle must be determined from its manufacturer. But for purposes of example we will assume a spindle quality of G2.5, which is the quality most often specified in machine tool drives. That dictates the tool/toolholder assembly must at least be balanced to that level. Assuming the tool/toolholder assembly weighs 5 pounds (2270 grams) and the desired spindle speed is 15,000 rpm, the formula below can be applied to determine the allowable unbalance.
The example above tells us that the tool/toolholder assembly should be equal to or less than 3.6 g/mm of unbalance for the assembly to work properly in a machine spindle of G2.5 quality. If the speed were to escalate to 20,000 rpm, the unbalance tolerance would drop to 2.7 g/mm. If the toolholder weighs only 2.5 pounds (1135 grams), then the unbalance tolerance drops to 1.8 g/mm at 15,000 rpm.
All of these unbalance tolerance numbers are in a very tight envelope of balance quality. Compare the numbers above with conventional-speed 40 taper V-flange holders. With unbalance in the 75-100 g/mm range and more, one can easily see the need to use nothing but holders that are balanced to the necessary specifications.
While getting to this quality of balance with reliable repeatability is not easy, Command Tooling Systems, working in conjunction with Makino, has developed a new premium balanced line of micro-precision collet holders and hydraulic gripping end mill holders that offer the necessary repeatable balance parameters. Always remember to use high-quality, symmetrical cutters that do not have flats on the shank. Also, clean everything before assembling the cutter-collet-holder combination; if it’s a hydraulic holder, remember to clean the bore before installing the end mill.
A Perfect Fit
At any spindle speed, quality of the toolholder, in terms of spindle fit and concentricity, is very important. As spindle speeds continually reach faster "racetrack" levels, the toolholder quality directly impacts spindle fit and concentricity of the cutting tool. As a result, the toolholder should be properly balanced on a balancing machine to achieve the proper specifications and tolerances. And finally, you must make sure everything is clean during assembly, with a good symmetrical cutter that has no flats. By keeping these tips in mind, you’ll have a direct impact on your toolholders and the entire machining application.
Source: Competitive Mold Maker, Volume 3, Number 2