By the mid-eighties the machine tool and generator designs had changed dramatically. Unlike the early "sewing machines" the Wire EDM machine had developed into a machine tool.
Though the basic concept of metal removal is the same as on a Die Sinker, a Wire EDM machine, by its very design is quite different. For instance, all Wire EDM machines are CNC controlled while there are both manual and CNC Die Sinkers.
Performance jumped from 1 to 6 and then 12 in2/hr. Competition between EDM manufacturers continued through the eighties and performance improved.
Today, CNC Wire manufacturers boast "advertised" first pass machining rates in excess of 25 in2/hr.
High current generators, higher flushing pressures requiring stiffer, more rigid tooling and premium wire (electrodes) have all had an impact on cutting speeds.
Basic Wire EDM Machines
Unlike conventional Die Sinkers, Wire EDM machining centers always operate with extremely small electrode contact area. Because of this small electrode contact area the average current that may be applied to the Wire is small in comparison.
Because of the very nature of Wire EDM machines they demand higher maintenance than a conventional Die Sinker.
The Wire transport system, Wire guides, automatic wire threader and dielectric systems are critical to the productivity of a Wire EDM machine.
The basic Wire EDM today offers 4- or 5-axis (X, Y, U, V & Z) positioning capability in order to perform complex taper or three-dimensional machining.
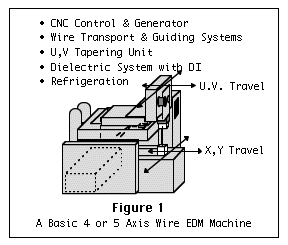
A Basic 4 or 5-Axis Wire EDM Machine Center
The upper head can be offset in the U & V axis tipping the Wire at an angle to the lower guide. The Wire spool, pulleys, auto threading "Jet" and clutch that provides accurate wire tensioning are located on the upper head.
Any problem with this drive system will impact the way in which the wire machines a part.
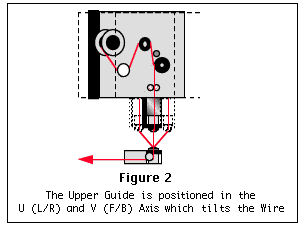
Tapering is accomplished by shifting the U and the V axis from the X and Y table (part) position.
This taper capability makes CNC Wire EDM ideal for producing a wide variety of parts. It makes it possible to machine draft and clearance on mold or die components, as well as machining of complex production parts.
The upper and lower heads each contain a Wire guide and energizing plate that must be monitored for wear and cleaned on a regular basis, usually about once a week.
Current is transmitted to the wire through the energizer plates. These (carbide) plates wear faster when machining rates increase.
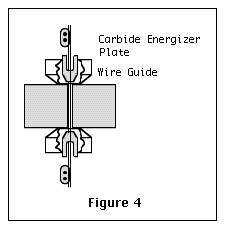
Lower Wire Guides and energizer plates may wear faster than those in the upper head. Debris from the cut, and wire shavings, can cause the guides to become clogged which, in turn, may cause wire breakage or cause the Automatic Threader to fail to operate.
Dielectric Systems
Deionized water is usually used as the dielectric so that high-pulse frequencies can be achieved. The dielectric filtering and Deionizing system play a key role in preventing excessive wire breakage. (Note: Dielectric oil is available as a dielectric on some machines. Ionization of the oil is much slower than DI water causing a substantial decrease in machining speed.)
Deionized water is the principle dielectric medium used on Wire EDM machine centers. Water is used to push chips and debris out of the Wire slot and cool the Wire and workpiece.
Since water is not the insulator that dielectric oil can be, ionization occurs rapidly. Because of this, water will retain current even after the voltage is turned off.
Resins help to maintain the conductivity level of the water. This conductivity level is described as Microsiemens (s) and the desired level of conductivity that should be maintained for a given application may vary from material to material.
If the conductivity level is too high during machining you may experience excessive Wire breakage.
Dielectric flushing pressures have been increased (i.e., up to 300 psi) over the past few years in order to boost cutting speed.
These higher pressures coupled with advances in power supplies and Wire composition have all had a major impact on machining speed.
Cutting Speed
As stated before, EDM Die Sinkers can operate at high average currents (i.e., above 100 Amps when using large electrodes). A Wire EDM machine is limited to the amount of average current that can be used due to the small contact area of the (Wire) electrode.
The first Wire EDM machine centers were slow by today’s standards, rated at a mere 1-1/2 to 2 in2/hr machining speeds. Unlike Die Sinkers, these early machines were extremely delicate instruments. Even at these slow machining rates, Wire EDM opened up whole new applications for EDM.
The EDM process is not "magic". With these improvements in machining rates we must keep in mind that the accuracy and precision of the initial (roughing) operation will determine the number of subsequent operations (i.e., skim cuts).
"Total time as it relates to part quality is the key to machining performance!"
There are a number of things that can influence the machining speed of a CNC Wire EDM Machine Center:
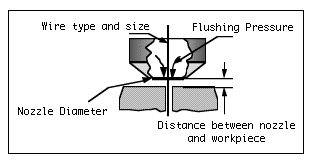
Slower |
Faster |
|
1. Water Pressure |
Lower |
High |
2. Wire Type |
Brass |
Coated |
3. Wire Diameter |
Smaller |
Larger |
4. Wire Tension |
Taut |
Loose |
5. Nozzle Distance |
Close |
Far Away |
Figure 5
Things that Impact Machining Speed
The surface area of the Wire will determine the average amperage that can be applied to the cut. As the Wire diameter becomes smaller or the workpiece thinner, the amount of current that can be applied to the cut drops.
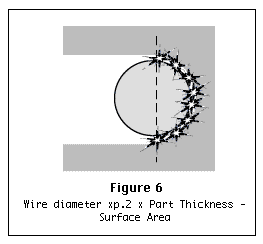
Though it stands to reason that a larger Wire diameter will provide better cutting speed there are other things to consider.
For example, accuracy may be adversely affected the faster you machine. Overall downtime replacing worn contacts and general upkeep will also increase, not to mention the overall consumption of the Wire itself.
Wire Diameter |
.008" |
.010" |
.012" |
Feet per Pound |
5,200 ft |
3,300 ft |
2,200 ft |
Wire Feed Rate |
6 ips |
6 ips |
5 ips |
Avg. Usage per Hour |
|
|
|
Length |
1,800 ft |
1,800 ft |
1,500 ft |
Weight |
.35 lbs |
.55 lbs |
.68 lbs |
Wire is not the only consumable that is used faster as machining increases. Wire contacts, DI resin, filters and guides are all consumed at a faster rate. Higher maintenance can be expected which results in some machine downtime.
Obviously the earning capacity of a CNC EDM machine center is more valuable than a few dollars worth of Wire unless the Wire is simply being wasted. Depending upon the Wire being used, the few dollars an hour can translate into thousands of dollars a year.
The type of Wire will also impact overall cost and performance. Though standard brass is used more than any other Wire type by a large margin (up to 75%), premium coated Wires offer enhanced performance for certain types of applications.
The outer coating melts rapidly cooling the Wire and increasing the size of the spark gap, providing better flushing.
Sold by the pound, EDM Wire costs between $4 a pound for brass to $12 $14 a pound for premium Wires. The chart above gives an example of Wire consumption that can be used to calculate costs.
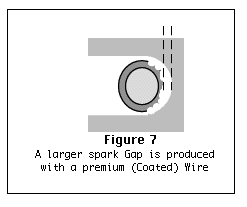
It is important to match the correct tool with the application. It is just as important to prevent throwing your money away.
Automatic Wire Threading
Probably the most important development for Wire EDM machines in terms of real productivity was the invention of the Automatic Wire Threader (AWT).
As the story goes, the original auto-threader was developed in the early eighties by an EDM job shop in Europe that was dissatisfied with the productivity of their one Wire EDM machine.
Though early Automatic Wire Threaders were not known for high reliability, when they worked, they provided superior throughput over a machine without one.
The Automatic Wire Threader made it possible for work to be scheduled into the Wire EDM machine based upon the needs of the operator rather than the length (time) of cut.
In general, the auto-threader alone can improve your capital equipment pay back on a Wire machine by 2 or 3:1.
Improved productivity is only one benefit to the threader. The flexibility in how the operator might approach a specific application, or how one might program a difficult job, can be enhanced by taking full advantage of an AWT system.
If, for instance, the part to be machined is going to "move" prior to skim cutting you might consider machining the part in steps using multiple start (auto-thread) locations to hold the part firmly in place. Accuracy and surface finish can also be improved in just such an application.
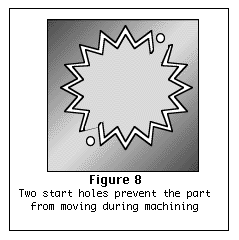
Most threaders today utilize a water jet system to transport the Wire between the upper and lower guides.
Because of the small size of the Wire electrode and the complexity of the entire transport system, the Automatic Wire Threader must be maintained according to the manufacturer’s recommendations.
Failure to properly clean or maintain this valuable machine feature will cause lost production time and money.
Generator
Unlike a Die Sinker that uses long On-Times during roughing operations a Wire EDM uses peak current for very short duration in order to machine a part.
The Wire EDM cut uses high (peak) current pulses with short On-Times and relatively short Off-Times times. The result is that extremely high spark frequency is achieved.
Since deionized water is used as a dielectric instead of oil (which is a true insulator) there is much less concern over Delay-Time (during ionization). Even though resin is used to deionize the water it does remain charged following an EDM pulse. This leads to a problem known as electrolysis.
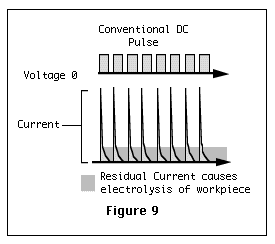
As machining current is applied in the cut the water becomes charged.
Residual current stays in the water continually eating away at the workpiece. This electrochemical reaction in the work tank can cause damage to the integrity of a part. The part’s surface can be damaged or discolored and rust may form.
Electrolysis will adversely affect the work material, causing unwanted pitting and cracking in tool steels or causing cobalt depletion in carbide. Depending upon the application and use of the part being produced, premature failure may be the end result.
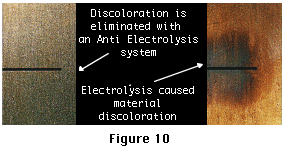
By alternating the voltage, residual current is eliminated thus preventing the water from remaining charged and causing electrolysis and oxidation of the workpiece.
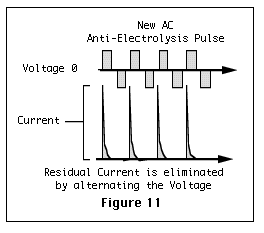
As can be seen, there are fewer pulses per length of time using this type of pulse generation. It makes sense that the machine will cut slower. It may be worth machining slower if the part produced is better and lasts longer.
Accuracy
Accuracy, like any other machining process, must be considered at the beginning of the job. The way in which a part is rough machined will have some impact on how long finishing takes.
If we push the Wire through a thicker workpiece at the fastest possible speed we will probably produce a bow or belly in the part after the first pass.
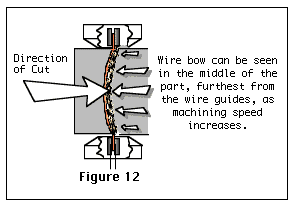
If the deviation in the middle of the part is excessive it may be very difficult to correct with secondary "skim" passes.
Since the Wire is flexible even under tension and does not physically contact the work, it may simply bend or bow to the existing shape when skimming the part. The sparks will push the Wire away from the work, recutting the existing shape.
Though putting more "tension" on the Wire may help to eliminate some of the problem, it may also increase the number of Wire breaks.
Even if skim cutting is successful, the number of passes to eliminate the error may take longer. If the initial roughing pass is slower, producing a more accurate part to begin with, fewer skims are necessary.
Similar to conventional machining, if the first cut is too rough (inaccurate) you can expect to spend more time finishing the piece.
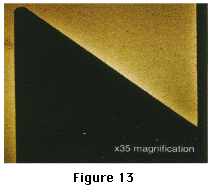
Corner accuracy is another area that newer Wire EDM machines have addressed well.
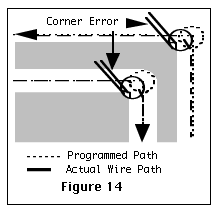
Though older Wire EDM machines can produce very accurate pieces, the cutting speed of newer machines has caused problems with corner accuracy. Machining a 2.00" thick piece at a cutting rate 25in2/hr will not produce an accurate corner.
No one will ever accuse Wire EDM machining centers of being fast when compared to a High Speed Machining Center. Therefore it is obvious that corner inaccuracy is not caused by overshoot of the servo drive system.
The problem is caused by the position of the thin Wire electrode after it leaves the guide. Once the Wire enters the workpiece the same force that can cause bow or belly in the part also pulls the Wire out of location. This can result in leaving excess stock on an inside corner and gouging an outside corner.
Though systems and/or software have been developed to counteract this problem, it will only correct the Wire error near the guide. It will not necessarily correct the shape in the middle of a (thicker) piece.
Depending upon the application, improved corner accuracy can be enhanced by altering the programmed shape in some way.
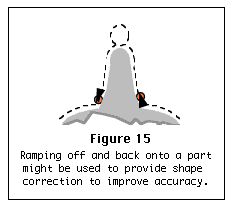
Even with advanced controls and programming systems, some applications may still require some form of (programmed) path correction. It can take time and multiple test cuts to get a modified programmed shape just right.
Tooling
Several years ago it was not uncommon for Wire EDM tooling to sit unused in a box. After all, what would you do with all that tooling if you didn’t have an Automatic Wire Threader.
There really isn’t much need to incorporate multiple setups on a machine table if threading is manually performed.
The average shop used "one part on; one part off" type of operation!
With the proliferation of auto-threaders over the past few years the need for a systematic approach to tooling not only seemed appropriate, but was necessary.
Original systems designed for Wire EDM machines worked well up until flushing pressures increased dramatically in order to boost cutting speeds.
When machining rates reached 20 in/hr it became apparent that the tooling had to be strengthened.
First, it was difficult to hold a part firmly because of the overhang of the part into the workzone. Secondly, the additional flushing pressures during roughing combined with the overhang caused excessive vibration, and therefore problems maintaining accuracy.
Wire EDM Tooling is far more rugged today than ever before and also provides the user the ability to totally integrate the manufacturing process between multiple machines.
With enhanced machine and tooling repeatable accuracies (1 to 2 microns) it has become easier to move parts from machine to machine very accurately, opening up a whole new realm of possibilities.
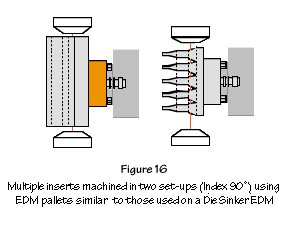
Learning Is Key
Regardless of how many years of experience one acquires in EDM, there are always new things to learn! New technology and so many (EDM) variables force all of us to continually challenge ourselves.
It seems that new applications appear every day for EDM, and therefore new learning opportunities, even for the most experienced operator.
There is no single source of information that has all the (EDM) answers. No one individual or organization that knows it all, though we might like to think we do!
Regardless of who you are, or the number of years under your belt, remaining inquisitive and keeping an open mind may be the most valuable EDM tool you own.
After all, experience is the teacher that trains us all!